Best PDC Cutter for Optimal Performance
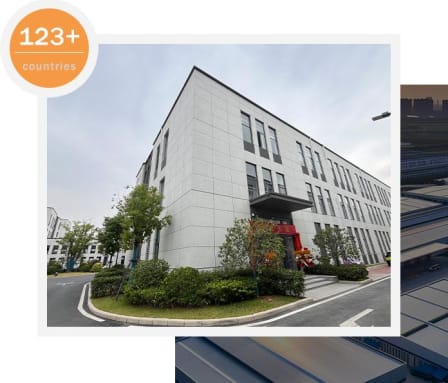
# Best PDC Cutter for Optimal Performance
When it comes to drilling operations, selecting the best PDC cutter can make a significant difference in performance, efficiency, and cost-effectiveness. Polycrystalline Diamond Compact (PDC) cutters are widely used in oil and gas drilling, mining, and other industrial applications due to their exceptional hardness and durability. In this article, we will explore the key factors to consider when choosing the best PDC cutter for your needs.
## What is a PDC Cutter?
A PDC cutter is a synthetic diamond compact that is bonded to a tungsten carbide substrate. This combination creates a cutting tool that is extremely hard and resistant to wear, making it ideal for demanding drilling environments. The diamond layer provides the cutting edge, while the carbide substrate offers structural support and thermal stability.
## Key Features of the Best PDC Cutter
### 1. Diamond Quality
The quality of the diamond layer is crucial for the performance of a PDC cutter. High-quality diamonds with uniform grain size and minimal impurities ensure better cutting efficiency and longer lifespan.
### 2. Substrate Material
The tungsten carbide substrate must be of high quality to provide adequate support to the diamond layer. A well-engineered substrate enhances the cutter’s thermal stability and impact resistance.
### 3. Geometry and Design
The shape and design of the PDC cutter play a vital role in its performance. Different geometries are suited for specific drilling conditions, such as soft or hard formations.
### 4. Thermal Stability
Keyword: best pdc cutter
Drilling generates significant heat, so the best PDC cutters are designed to withstand high temperatures without degrading. Thermal stability ensures consistent performance even under extreme conditions.
## Top Applications of PDC Cutters
PDC cutters are used in various industries, including:
– Oil and gas drilling
– Mining and exploration
– Geothermal drilling
– Construction and tunneling
## How to Choose the Best PDC Cutter
Selecting the right PDC cutter depends on several factors:
– Formation type: Soft, medium, or hard formations require different cutter designs.
– Drilling conditions: Consider factors like temperature, pressure, and abrasiveness.
– Bit design: The cutter must be compatible with the bit’s design and configuration.
– Budget: Balance performance requirements with cost considerations.
## Maintenance and Longevity
To maximize the lifespan of your PDC cutters, proper maintenance is essential. Regular inspections, proper storage, and using the right drilling parameters can significantly extend the cutter’s operational life.
## Conclusion
Choosing the best PDC cutter is critical for achieving optimal drilling performance. By considering factors like diamond quality, substrate material, geometry, and thermal stability, you can select a cutter that meets your specific needs. Investing in high-quality PDC cutters can lead to improved efficiency, reduced downtime, and lower overall drilling costs.