Injection Molding Process Optimization for Enhanced Manufacturing Efficiency
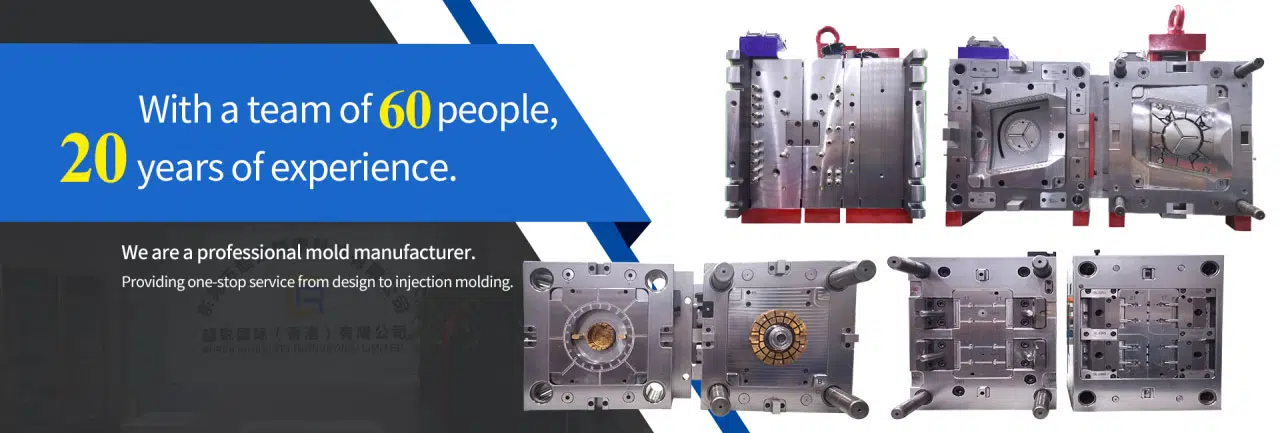
html
Injection Molding Process Optimization for Enhanced Manufacturing Efficiency
Keyword: Injection Molding
Injection molding is a widely used manufacturing process for producing plastic parts in large volumes. It involves injecting molten material into a mold, where it cools and solidifies into the desired shape. To maximize efficiency and reduce costs, optimizing the injection molding process is essential. This article explores key strategies for improving manufacturing efficiency through process optimization.
Key Factors Affecting Injection Molding Efficiency
Several factors influence the efficiency of the injection molding process. Understanding these variables is the first step toward optimization:
- Material Selection: Choosing the right polymer for the application can reduce cycle times and improve part quality.
- Mold Design: A well-designed mold minimizes defects and ensures consistent production.
- Machine Parameters: Proper settings for temperature, pressure, and injection speed are critical for efficiency.
- Cycle Time: Reducing cycle time without compromising quality is a primary goal of optimization.
Strategies for Process Optimization
To enhance manufacturing efficiency, consider implementing the following strategies:
1. Advanced Mold Design
Investing in high-quality mold design with features like conformal cooling channels can significantly reduce cycle times. These channels allow for more uniform cooling, minimizing warping and defects.
2. Automation and Robotics
Integrating automation into the injection molding process can streamline operations, reduce labor costs, and improve consistency. Robotic systems can handle tasks such as part removal, inspection, and packaging.
3. Real-Time Monitoring
Using sensors and IoT-enabled devices to monitor machine performance in real-time helps identify inefficiencies and prevent downtime. Data analytics can provide insights for further optimization.
4. Material Optimization
Selecting materials with faster cooling rates or lower viscosity can improve cycle times. Additionally, recycling scrap material can reduce waste and lower production costs.
Benefits of Optimized Injection Molding
Optimizing the injection molding process offers several advantages:
- Reduced Production Costs: Efficient processes lower material waste and energy consumption.
- Higher Output Rates: Shorter cycle times enable faster production.
- Improved Part Quality: Consistent processes result in fewer defects.
- Sustainability: Reduced waste and energy use contribute to environmentally friendly manufacturing.
Conclusion
Injection molding process optimization is a continuous effort that requires attention to detail and a willingness to adopt new technologies. By focusing on mold design, automation, real-time monitoring, and material selection, manufacturers can achieve significant improvements in efficiency and product quality. Implementing these strategies not only enhances productivity but also supports sustainable manufacturing practices.