High-Precision Machining Technology and Its Applications
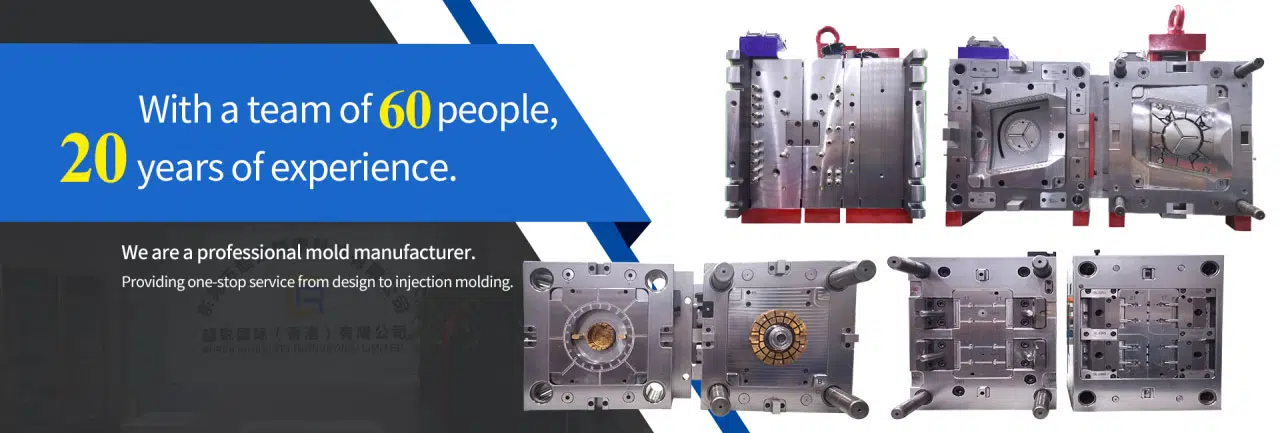
,字数要求1000字左右
html
High-Precision Machining Technology and Its Applications
High-precision machining is a critical manufacturing process that enables the production of components with extremely tight tolerances and superior surface finishes. This technology plays a vital role in industries where accuracy and reliability are paramount, such as aerospace, medical devices, and automotive engineering.
The Fundamentals of High-Precision Machining
At its core, high-precision machining involves removing material from a workpiece to create parts with dimensional accuracy often measured in micrometers. The process typically utilizes advanced CNC (Computer Numerical Control) machines that can achieve tolerances as tight as ±0.001 mm or better.
Key elements that contribute to high-precision machining include:
- State-of-the-art machine tools with minimal vibration and thermal distortion
- Advanced cutting tools made from ultra-hard materials
- Precision measuring instruments and quality control systems
- Stable environmental conditions (temperature, humidity control)
- Highly skilled operators and programmers
Advanced Techniques in High-Precision Machining
Micro-Machining
This specialized form of high-precision machining deals with creating extremely small features, often requiring specialized equipment that can handle tools with diameters as small as 0.001 inches. Micro-machining is essential for producing medical implants, microelectronics, and optical components.
Ultra-Precision Turning
Using diamond-tipped tools on specially designed lathes, ultra-precision turning can achieve surface finishes with roughness values below 10 nanometers. This technique is particularly valuable for manufacturing optical components and precision bearings.
5-Axis Machining
The ability to move a workpiece or cutting tool along five different axes simultaneously allows for the creation of complex geometries with exceptional accuracy. This method significantly reduces setup times and improves overall precision.
Materials Used in High-Precision Machining
High-precision machining can work with a wide range of materials, each presenting unique challenges:
Material Type | Common Applications | Machining Considerations |
---|---|---|
Metals (Aluminum, Titanium, Steel) | Aerospace components, medical devices | Tool wear, heat generation |
Plastics (PEEK, Delrin) | Medical implants, electronic components | Thermal expansion, static buildup |
Ceramics | Cutting tools, bearings | Brittleness, specialized tooling |
Composites | Aerospace structures | Delamination, fiber orientation |
Applications of High-Precision Machining
Aerospace Industry
The aerospace sector relies heavily on high-precision machining for turbine blades, fuel system components, and structural parts. The extreme operating conditions of aircraft demand components manufactured to exacting standards with exceptional reliability.
Medical Device Manufacturing
Surgical instruments, implants, and diagnostic equipment all benefit from high-precision machining. The ability to create complex, biocompatible components