Flange Facer Machine Solutions for Industrial Applications
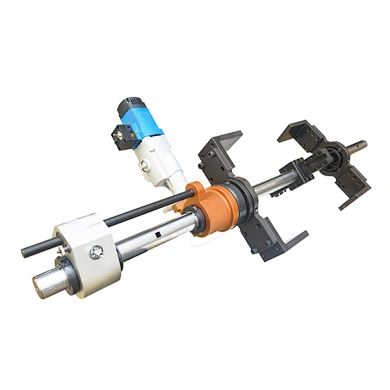
# Flange Facer Machine Solutions for Industrial Applications
## Introduction to Flange Facer Machines
Flange facer machines are essential tools in various industrial applications, particularly in the oil and gas, petrochemical, and power generation industries. These machines are designed to resurface and repair damaged flange faces, ensuring proper sealing and alignment for piping systems. With precision engineering and robust construction, flange facers help maintain the integrity of critical infrastructure.
## Key Features of Modern Flange Facer Machines
Today’s flange facer machines incorporate several advanced features that make them indispensable for industrial maintenance:
- Portable designs for on-site flange facing operations
- Variable speed control for optimal surface finishing
- Automatic feed systems for consistent results
- Versatile tooling options for different flange types
- Durable construction for heavy-duty applications
## Applications Across Industries
Oil and Gas Sector
In the oil and gas industry, flange facers are crucial for maintaining pipeline integrity. They’re used to repair flange faces damaged by corrosion, erosion, or improper installation, preventing costly leaks and downtime.
Keyword: flange facer machines
Power Generation Plants
Power plants rely on flange facers to maintain steam and water piping systems. Properly faced flanges ensure leak-free connections in high-pressure environments, contributing to plant safety and efficiency.
Chemical Processing
The chemical industry uses these machines to maintain flange surfaces that must withstand aggressive chemicals and extreme temperatures while maintaining perfect seals.
## Choosing the Right Flange Facer Machine
When selecting a flange facer machine, consider these factors:
- Flange size range capability
- Power source requirements (electric, hydraulic, or pneumatic)
- Material compatibility
- Portability and setup time
- Available accessories and tooling options
## Maintenance and Safety Considerations
Regular Maintenance
Proper maintenance of flange facer machines includes regular lubrication, tool sharpening, and inspection of moving parts. Following manufacturer guidelines ensures optimal performance and longevity.
Safety Protocols
Operators should always wear appropriate PPE, secure workpieces properly, and follow lockout/tagout procedures when servicing equipment. Proper training is essential for safe operation.
## Conclusion
Flange facer machines provide reliable solutions for maintaining critical piping connections across various industries. By investing in quality equipment and proper training, facilities can ensure leak-free operations, reduce downtime, and extend the life of their piping systems. As technology advances, these machines continue to evolve, offering greater precision and efficiency for industrial applications.